Conteúdo
- 1 Kaizen, Sistema Toyota de Produção (STP) e a Gestão da Qualidade Total (TQM)
- 2 Semelhanças e postos-chave da filosofia Kaizen e do Processo de Raciocínio da Teoria das Restrições (TOC)
- 3 Kaizen: ferramentas e técnicas para a solução de problemas e melhoria contínua
- 3.1 Ciclo PDCA (Plan-Do-Check-Act)
- 3.2 Metodologia 5S
- 3.3 Ishikawa (Diagrama de Espinha de Peixe)
- 3.4 Análise de Pareto
- 3.5 Kaizen Blitz (Kaizen em eventos)
- 3.6 Gemba (ou Genba) Walk
- 3.7 Kanban
- 3.8 Standard Work (Trabalho Padronizado)
- 3.9 Total Productive Maintenance (TPM)
- 3.10 Heijunka (Nivelamento de Produção)
- 4 Filosofia Kaizen e Sistema Toyota de Produção
Kaizen é uma filosofia japonesa de melhoria contínua que se concentra em fazer pequenas mudanças incrementais e consistentes para melhorar a eficiência e a qualidade dos processos e produtos. A palavra “Kaizen” é derivada de duas palavras japonesas: “kai” (mudança) e “zen” (bom ou para melhor), significando “mudança para melhor”.
O conceito de Kaizen se baseia na ideia de que a melhoria constante e gradual pode levar a resultados significativos a longo prazo. A filosofia Kaizen é aplicada em muitas organizações, incluindo manufatura, saúde, negócios e educação.
Os principais princípios do Kaizen incluem:
- Foco na melhoria contínua: Em vez de buscar melhorias radicais ou revolucionárias, o Kaizen enfatiza a importância de fazer pequenas melhorias de forma consistente ao longo do tempo.
- Envolvimento de todos: O Kaizen incentiva a participação de todos os membros da organização, independentemente do cargo ou função. Cada pessoa é incentivada a identificar oportunidades de melhoria e propor soluções.
- Identificação e eliminação de desperdícios: A filosofia Kaizen visa identificar e eliminar desperdícios e ineficiências em processos e sistemas. O desperdício pode ser definido como qualquer atividade que não agrega valor ao produto final ou serviço.
- Padronização: A padronização é uma parte fundamental do Kaizen, pois facilita a comparação de desempenho, a identificação de problemas e a implementação de melhorias.
- Resolução de problemas na fonte: O Kaizen se concentra em resolver problemas na fonte, em vez de apenas tratar os sintomas. Isso inclui identificar a causa raiz dos problemas e implementar soluções para prevenir sua recorrência.
- Aprendizado e adaptação: A filosofia Kaizen enfatiza a importância do aprendizado contínuo e da adaptação à medida que as condições mudam. Isso envolve o compartilhamento de conhecimentos e a adoção de novas ideias e tecnologias.
Ao aplicar a filosofia Kaizen, as organizações podem melhorar continuamente seus processos e produtos, aumentar a eficiência e a qualidade e promover uma cultura de inovação e melhoria contínua.
Quem criou a filosofia Kaizen?
Não há um único criador atribuído à filosofia Kaizen. Em vez disso, o Kaizen tem suas raízes em várias práticas e ideias japonesas e, em parte, na influência americana após a Segunda Guerra Mundial. A filosofia Kaizen tem sido desenvolvida e refinada ao longo do tempo, e muitos indivíduos e organizações contribuíram para sua evolução.
Uma figura-chave na popularização do Kaizen é Masaaki Imai, um consultor de gestão japonês e especialista em qualidade. Ele é o autor do livro “Kaizen: The Key to Japan’s Competitive Success”, publicado em 1986, que ajudou a difundir a filosofia Kaizen no mundo dos negócios ocidentais.
O livro de Imai descreve os princípios e práticas fundamentais do Kaizen e fornece exemplos de como ele foi aplicado com sucesso em empresas japonesas.
Além disso, a filosofia Kaizen também foi influenciada por práticas de gestão e qualidade, como o Sistema Toyota de Produção e a Gestão da Qualidade Total (TQM), que também se concentram na melhoria contínua e na eliminação de desperdícios. Esses sistemas e práticas compartilham muitos princípios com o Kaizen e têm sido importantes no desenvolvimento e na disseminação dessa filosofia.
Kaizen, Sistema Toyota de Produção (STP) e a Gestão da Qualidade Total (TQM)
O Sistema Toyota de Produção (STP) e a Gestão da Qualidade Total (TQM) são duas abordagens de gestão e qualidade que influenciaram e compartilham princípios com a filosofia Kaizen.
Vamos examinar cada uma delas:
- Sistema Toyota de Produção (STP): Também conhecido como “Lean Manufacturing” ou “Produção Enxuta”, o STP foi desenvolvido pela Toyota Motor Corporation no Japão, principalmente por Taiichi Ohno e Eiji Toyoda. O objetivo do STP é aumentar a eficiência e eliminar o desperdício (chamado “muda” em japonês) nos processos de produção. O STP incorpora várias práticas e conceitos chave que se alinham e influenciaram o Kaizen, como:
- Just-in-Time (JIT): Produção e entrega de produtos conforme necessário, reduzindo estoques e otimizando a utilização de recursos.
- Jidoka: Autonomia para identificar e corrigir problemas no processo de produção, muitas vezes concedendo aos trabalhadores a autoridade para interromper a linha de produção caso encontrem problemas de qualidade.
- Padronização: Estabelecimento de procedimentos e processos padrão para garantir a consistência e a qualidade do produto.
- Melhoria contínua: Enfatizando a busca constante por melhorias nos processos de produção e na qualidade do produto.
- Gestão da Qualidade Total (TQM): A TQM é uma abordagem de gestão que se concentra na melhoria contínua da qualidade dos produtos e processos de uma organização. A TQM enfatiza a participação de todos os membros da organização e se concentra na satisfação do cliente. Alguns princípios da TQM que influenciaram o Kaizen incluem:
- Envolvimento de todos: A TQM incentiva a participação de todos os funcionários na melhoria contínua da qualidade e reconhece que a responsabilidade pela qualidade não se limita apenas a um departamento ou função específica.
- Foco no cliente: A TQM coloca a satisfação do cliente no centro das decisões e busca atender e exceder suas expectativas.
- Melhoria contínua: A TQM promove a busca constante por aprimoramentos na qualidade do produto e nos processos da organização.
- Medição e análise: A TQM enfatiza a importância de medir o desempenho e usar dados para identificar áreas de melhoria e tomar decisões baseadas em fatos.
Tanto o STP quanto a TQM compartilham a ênfase na melhoria contínua, na eliminação de desperdícios e na participação de todos os membros da organização.
Esses princípios e práticas foram incorporados à filosofia Kaizen, contribuindo para sua evolução e popularização. Juntos, eles formam um conjunto abrangente de abordagens e ferramentas para otimizar processos e melhorar a qualidade em uma ampla variedade de organizações e setores.
Você já viu nossa postagem sobre a Teoria das Restrições e Processo de Raciocínio: Uma Abordagem para Melhoria Contínua ? Acesse e leia todo o artigo.
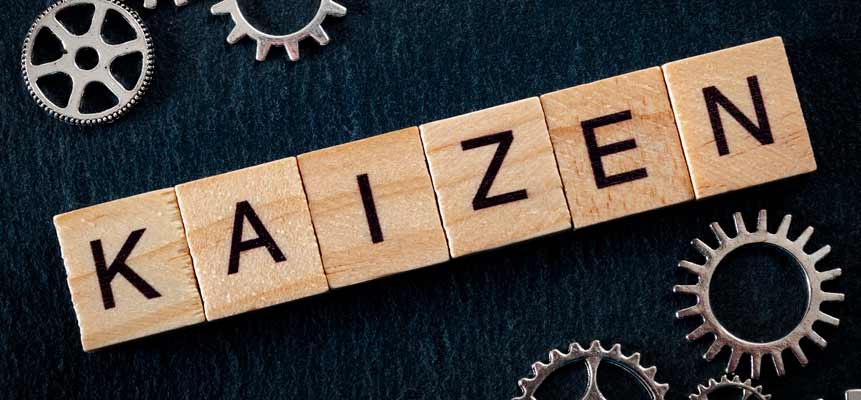
Semelhanças e postos-chave da filosofia Kaizen e do Processo de Raciocínio da Teoria das Restrições (TOC)
Ambas as abordagens, Kaizen e TOC, buscam melhorar continuamente os processos e a eficiência organizacional, mas a filosofia Kaizen se concentra em melhorias incrementais em toda a empresa, enquanto o Processo de Raciocínio da TOC foca nas restrições do sistema.
Apesar das diferenças, as duas metodologias podem ser complementares e aplicadas juntas para maximizar os resultados.
Aspecto | Filosofia Kaizen | Processo de Raciocínio da TOC |
---|---|---|
Objetivo | Melhoria contínua em todos os aspectos | Melhoria contínua focada nas restrições |
Abordagem | Incremental e evolutiva | Sistemática e focada |
Participação | Envolvimento de todos os funcionários | Pode envolver todos os níveis da organização |
Identificação | Identificar áreas de melhoria em toda a empresa | Identificar restrições no sistema |
Solução de problemas | Uso de ferramentas como ciclo PDCA, 5S, etc. | Utilização do Processo de Raciocínio |
Foco | Qualidade, eficiência e satisfação do cliente | Maximizar o throughput e reduzir o lead time |
Monitoramento | Acompanhamento constante e ajustes | Medição e avaliação do desempenho |
Cultura | Cultura de melhoria contínua e aprendizado | Cultura de gerenciamento de restrições |
Kaizen: ferramentas e técnicas para a solução de problemas e melhoria contínua
A filosofia Kaizen utiliza várias ferramentas e técnicas para a solução de problemas e melhoria contínua, a maioria delas tem origem com a criação, desenvolvimento e aperfeiçoamento do Sistema Toyota de Produção (STP). Conheça algumas das ferramentas mais populares incluem:
Ciclo PDCA (Plan-Do-Check-Act)
Ciclo PDCA (Plan-Do-Check-Act): Um método iterativo de quatro etapas para a melhoria contínua, envolvendo planejamento, execução, verificação e ajuste com base nos resultados.
O Ciclo PDCA (Plan-Do-Check-Act) foi desenvolvido pelo Dr. Walter A. Shewhart, um físico e estatístico americano que trabalhava nos Laboratórios Bell nos anos 1920 e 1930.
No entanto, o ciclo PDCA ficou mais conhecido e amplamente adotado após ser popularizado por outro estatístico americano, Dr. W. Edwards Deming, na década de 1950. Deming aplicou o PDCA como uma parte fundamental de sua filosofia de gerenciamento de qualidade, especialmente no Japão, onde ele teve uma grande influência no desenvolvimento das práticas de gerenciamento de qualidade após a Segunda Guerra Mundial. Por isso, o ciclo PDCA também é conhecido como Ciclo de Deming ou Ciclo de Shewhart-Deming.
O relacionamento entre o Ciclo PDCA e a filosofia Kaizen pode ser rastreado até as décadas de 1950 e 1960, quando a indústria japonesa começou a adotar e adaptar práticas de gerenciamento de qualidade dos EUA em um esforço para reconstruir e melhorar sua economia após a Segunda Guerra Mundial.
Dr. W. Edwards Deming, que popularizou o Ciclo PDCA, desempenhou um papel fundamental na introdução de suas ideias no Japão. Durante esse período, ele realizou várias palestras e seminários para empresários e engenheiros japoneses, incentivando a adoção do PDCA como uma ferramenta para a melhoria contínua. Em resposta, muitas empresas japonesas começaram a incorporar o PDCA em seus sistemas de gerenciamento de qualidade.
Paralelamente, a filosofia Kaizen estava ganhando força no Japão, influenciada pelas práticas de gerenciamento do Sistema Toyota de Produção e pela Gestão da Qualidade Total (TQM). A filosofia Kaizen enfatiza a melhoria contínua e incremental, envolvendo todos os membros da organização. O Ciclo PDCA se alinha bem com essa abordagem, fornecendo um método sistemático e iterativo para identificar, planejar, implementar e avaliar melhorias.
Assim, o relacionamento entre o Ciclo PDCA e a filosofia Kaizen começou a se solidificar nas décadas de 1950 e 1960, à medida que as empresas japonesas adotavam ambas as abordagens para melhorar a qualidade e a eficiência de seus processos e produtos.
Metodologia 5S
5S: Uma metodologia para a organização e manutenção do local de trabalho, composta por cinco etapas: Seiri (organização), Seiton (ordenação), Seisou (limpeza), Seiketsu (padronização) e Shitsuke (disciplina).
A metodologia 5S foi desenvolvida no Japão durante a década de 1950, como parte das práticas de gerenciamento do Sistema Toyota de Produção. Embora não seja atribuída a um único indivíduo, a metodologia 5S é geralmente associada à Toyota Motor Corporation e a seu sistema de produção pioneiro.
O Sistema Toyota de Produção, desenvolvido por Taiichi Ohno e outros colaboradores, visava otimizar a eficiência e eliminar desperdícios na fabricação. A metodologia 5S surgiu como uma abordagem para manter um ambiente de trabalho organizado, limpo e eficiente, o que era considerado crucial para a execução bem-sucedida do sistema de produção.
Desde a sua criação, a metodologia 5S tem sido aplicada em muitas indústrias e contextos diferentes, tanto no Japão como em outros países, e continua a ser uma abordagem popular para a melhoria da eficiência e da qualidade no ambiente de trabalho.
Embora seja difícil identificar um momento específico em que o conceito 5S e a filosofia Kaizen se encontraram, é possível afirmar que essas duas abordagens se desenvolveram em paralelo e se complementam, à medida que a indústria japonesa adotava práticas de gerenciamento de qualidade e eficiência após a Segunda Guerra Mundial.
A filosofia Kaizen, como mencionado anteriormente, tem suas raízes no Sistema Toyota de Produção e na Gestão da Qualidade Total (TQM). Kaizen foca na melhoria contínua e incremental, envolvendo todos os membros da organização. O 5S, por outro lado, foi desenvolvido como parte do Sistema Toyota de Produção, com o objetivo de criar um ambiente de trabalho organizado, limpo e eficiente.
Assim, é provável que o encontro do 5S e da filosofia Kaizen tenha ocorrido durante o desenvolvimento e a evolução do Sistema Toyota de Produção e da TQM, principalmente nas décadas de 1950 e 1960. Ambas as abordagens compartilham um objetivo comum de melhorar a qualidade e a eficiência, e são frequentemente implementadas juntas em programas de melhoria contínua.
A combinação dessas duas abordagens pode proporcionar benefícios significativos para as organizações, uma vez que a implementação do 5S cria um ambiente de trabalho favorável para a aplicação do Kaizen. Com um local de trabalho organizado e eficiente, os membros da equipe podem se concentrar em identificar e solucionar problemas, reduzindo o desperdício e melhorando continuamente os processos e os resultados.
Ishikawa (Diagrama de Espinha de Peixe)
Uma ferramenta de análise de causa e efeito que ajuda a identificar as causas raiz dos problemas através da análise de diferentes categorias de possíveis causas.
A ferramenta de análise de causa e efeito, também conhecida como Diagrama de Ishikawa ou Diagrama de Espinha de Peixe, foi criada pelo engenheiro químico japonês Dr. Kaoru Ishikawa na década de 1960. Ishikawa desenvolveu essa ferramenta para ajudar as equipes a identificar e analisar as possíveis causas dos problemas em seus processos e produtos, facilitando a identificação de áreas que precisavam de melhorias.
Embora não exista uma data específica em que a ferramenta de análise de causa e efeito foi oficialmente reconhecida como parte da filosofia Kaizen, é importante notar que o Diagrama de Ishikawa se alinha bem com os princípios e objetivos do Kaizen. A filosofia Kaizen enfatiza a melhoria contínua, a solução de problemas e a redução de desperdícios, e o Diagrama de Ishikawa fornece uma estrutura visual para identificar as causas subjacentes dos problemas e encontrar soluções eficazes.
Ao longo dos anos, o Diagrama de Ishikawa tornou-se uma ferramenta amplamente utilizada na aplicação do Kaizen e em outras abordagens de gerenciamento de qualidade, como a Gestão da Qualidade Total (TQM) e o Seis Sigma. Sua eficácia e versatilidade o tornam uma parte importante das práticas de melhoria contínua em muitas organizações ao redor do mundo.
Análise de Pareto
A análise de Pareto é uma técnica estatística que se baseia no Princípio de Pareto (80/20) para identificar as causas mais importantes (20%) que levam a 80% dos problemas.
A Análise de Pareto é uma técnica que se baseia no Princípio de Pareto, também conhecido como a regra 80/20. Esse princípio foi desenvolvido pelo economista italiano Vilfredo Pareto no final do século XIX. Pareto observou que, em muitos casos, aproximadamente 80% dos efeitos são resultado de cerca de 20% das causas. Embora sua análise tenha se concentrado inicialmente na distribuição de renda e riqueza, o Princípio de Pareto provou ser aplicável a muitas áreas diferentes, incluindo a gestão da qualidade.
Não há uma data específica em que a Análise de Pareto se tornou oficialmente uma ferramenta da filosofia Kaizen. No entanto, a técnica começou a ser adotada na gestão da qualidade e na melhoria contínua durante o século XX. A análise de Pareto é uma ferramenta que complementa os princípios do Kaizen, pois ajuda a identificar as poucas causas fundamentais que têm o maior impacto nos problemas, permitindo que as equipes se concentrem em áreas de melhoria com o maior retorno potencial.
Ao longo do tempo, a Análise de Pareto tornou-se uma ferramenta comum em abordagens de melhoria contínua, como o Kaizen, o Seis Sigma e a Gestão da Qualidade Total (TQM). A aplicação da Análise de Pareto permite que as organizações priorizem suas ações de melhoria de forma eficiente, concentrando-se nas causas mais significativas dos problemas e nas oportunidades de melhoria mais relevantes.
Kaizen Blitz (Kaizen em eventos)
Kaizen Blitz é uma abordagem intensiva e de curto prazo para implementar melhorias em um processo específico, envolvendo uma equipe multidisciplinar trabalhando juntos em um período de tempo curto (geralmente uma semana).
O Kaizen Blitz, também conhecido como Kaizen Event ou evento Kaizen, é uma abordagem intensiva e focada de melhoria contínua que visa realizar mudanças significativas em um curto período de tempo, geralmente de três a cinco dias. A ferramenta Kaizen Blitz não pode ser atribuída a um único criador, mas sim ao desenvolvimento colaborativo de várias práticas japonesas de gestão e melhoria de qualidade ao longo do tempo, particularmente no contexto do Sistema Toyota de Produção.
O Kaizen Blitz foi adotado e adaptado por empresas e consultores de gerenciamento de qualidade em todo o mundo, especialmente a partir dos anos 1980 e 1990, quando a filosofia Kaizen e outras abordagens de melhoria contínua começaram a ganhar popularidade fora do Japão.
O Kaizen Blitz se tornou uma ferramenta da filosofia Kaizen por combinar os princípios fundamentais do Kaizen, como melhoria contínua, envolvimento dos funcionários e eliminação de desperdício, com uma abordagem de curto prazo e alta energia. Essa combinação permite que as equipes realizem mudanças rápidas e impactantes, trazendo resultados visíveis e imediatos para a organização e aumentando a motivação e o engajamento dos funcionários no processo de melhoria contínua.
Gemba (ou Genba) Walk
Uma prática onde a gerência visita o local de trabalho (gemba) para observar os processos em ação e identificar oportunidades de melhoria.
A ferramenta Gemba, também conhecida como Gemba Walk, não tem um único criador, mas é um conceito que se originou no Japão e é profundamente enraizado na cultura e práticas de gerenciamento japonesas, especialmente no contexto do Sistema Toyota de Produção. “Gemba” é uma palavra japonesa que significa “local real” ou “local onde o trabalho é realizado”. O Gemba Walk é uma prática na qual os gerentes e líderes visitam o local de trabalho para observar os processos em ação, identificar oportunidades de melhoria e interagir com os funcionários.
A prática do Gemba Walk se tornou uma ferramenta da filosofia Kaizen por estar alinhada com os princípios fundamentais do Kaizen, como o envolvimento dos funcionários, a melhoria contínua e a eliminação de desperdícios. Ao visitar o local de trabalho e observar os processos diretamente, os gerentes e líderes podem obter uma compreensão mais profunda dos problemas e desafios enfrentados pelos funcionários, permitindo que identifiquem e implementem melhorias eficazes.
Embora não haja uma data específica em que o Gemba Walk se tornou oficialmente parte da filosofia Kaizen, é provável que sua adoção tenha ocorrido de forma gradual, à medida que as práticas de gerenciamento e melhoria contínua japonesas se difundiram internacionalmente a partir dos anos 1980 e 1990. Hoje, o Gemba Walk é considerado uma prática essencial na aplicação bem-sucedida do Kaizen e é amplamente utilizado em organizações de diversos setores em todo o mundo.
Kanban
Kanban é um sistema visual de gestão de fluxo de trabalho que ajuda a equilibrar a demanda e a capacidade de produção, reduzindo estoques e aprimorando a eficiência.
Foi desenvolvido por Taiichi Ohno, o criador do o Sistema Toyota de Produção. Ohno criou o sistema Kanban como uma maneira de gerenciar o fluxo de trabalho e melhorar a eficiência na produção. O Kanban é uma ferramenta visual que ajuda a gerenciar e controlar o fluxo de trabalho em processos produtivos ou administrativos, promovendo a eficiência e a redução de desperdícios.
Embora o sistema Kanban tenha se originado no contexto do Sistema Toyota de Produção, ele se tornou uma ferramenta associada à filosofia Kaizen por ser um método eficaz de melhoria contínua. A abordagem visual e fácil de entender do Kanban ajuda as equipes a identificar gargalos e melhorar a comunicação. Além disso, ao limitar a quantidade de trabalho em andamento, o Kanban incentiva o foco na qualidade e na eliminação de desperdícios.
A adoção do sistema Kanban no âmbito da filosofia Kaizen ocorreu ao longo do tempo, especialmente a partir dos anos 1980 e 1990, quando a filosofia Kaizen e outras práticas de gerenciamento japonês ganharam popularidade fora do Japão. Hoje, o Kanban é amplamente utilizado em várias indústrias e setores como uma ferramenta eficaz para gerenciar fluxos de trabalho, melhorar a eficiência e promover a melhoria contínua.
Standard Work (Trabalho Padronizado)
A documentação e implementação de processos e procedimentos ideais para garantir a qualidade e a eficiência no trabalho. O conceito de Trabalho Padronizado (Standard Work) não pode ser atribuído a um único criador, pois é uma ideia que evoluiu ao longo do tempo, com várias pessoas e organizações contribuindo para o seu desenvolvimento.
A ideia básica de estabelecer padrões e procedimentos operacionais para garantir a qualidade e a eficiência tem suas raízes em várias práticas e teorias de gerenciamento, incluindo os princípios de administração científica de Frederick Taylor no início do século XX.
No entanto, o conceito de Trabalho Padronizado ganhou maior destaque no contexto do Sistema Toyota de Produção e da filosofia Lean. Taiichi Ohno e outros líderes da Toyota enfatizaram a importância da padronização e da melhoria contínua, combinando essas ideias com os princípios da eficiência e eliminação de desperdícios.
O Trabalho Padronizado se tornou uma ferramenta da filosofia Kaizen devido à sua ênfase na melhoria contínua, eficiência e eliminação de desperdícios. A padronização de processos e procedimentos de trabalho ajuda a estabelecer um ponto de partida para melhorias, proporcionando um ambiente em que os funcionários possam identificar e implementar melhorias nos processos.
A associação do Trabalho Padronizado com a filosofia Kaizen provavelmente ocorreu de forma gradual, à medida que o Sistema Toyota de Produção e a filosofia Lean se difundiram internacionalmente, principalmente a partir dos anos 1980 e 1990. Hoje, o Trabalho Padronizado é considerado uma prática essencial para a aplicação bem-sucedida do Kaizen e é amplamente utilizado em organizações de diversos setores em todo o mundo.
Total Productive Maintenance (TPM)
Trata-se de uma abordagem proativa para manutenção de equipamentos, envolvendo toda a organização, com o objetivo de aumentar a eficiência da produção e reduzir paradas.
A Total Productive Maintenance (TPM) é uma abordagem de manutenção preventiva que busca melhorar a produtividade e a eficiência das máquinas e equipamentos em uma organização. Embora não haja um único criador da TPM, ela foi desenvolvida e promovida no Japão na década de 1970, com o Japan Institute of Plant Maintenance (JIPM) desempenhando um papel importante na sua divulgação e implementação.
A TPM tem suas raízes no conceito de manutenção preventiva, que foi praticada pelos fabricantes americanos durante a década de 1950. A ideia foi então introduzida no Japão e desenvolvida ainda mais pelas indústrias japonesas, como parte da filosofia Lean e do Sistema Toyota de Produção. A TPM expandiu o escopo da manutenção preventiva tradicional, envolvendo todos os funcionários no processo de manutenção e melhoramento do desempenho dos equipamentos.
A conexão entre a TPM e a filosofia Kaizen se estabeleceu devido à ênfase compartilhada na melhoria contínua, eficiência e eliminação de desperdícios. A TPM promove a cultura de melhoria contínua ao incentivar a participação de todos os funcionários na manutenção e otimização dos equipamentos e processos produtivos. Além disso, a TPM ajuda a identificar e eliminar as causas de problemas de qualidade, tempo de inatividade e desperdício.
A TPM se tornou uma ferramenta da filosofia Kaizen principalmente nas décadas de 1980 e 1990, quando a filosofia Lean e o Sistema Toyota de Produção ganharam popularidade fora do Japão e foram adotados por organizações em todo o mundo. Atualmente, a TPM é amplamente reconhecida como uma prática importante para a aplicação bem-sucedida do Kaizen e é utilizada em várias indústrias e setores.
Heijunka (Nivelamento de Produção)
É uma técnica que visa equilibrar a carga de trabalho em todos os recursos e reduzir a variabilidade na produção.
Essas ferramentas são aplicadas em diferentes situações e processos, dependendo das necessidades e objetivos específicos da organização. A filosofia Kaizen incentiva a utilização e adaptação dessas ferramentas para promover a melhoria contínua e a solução de problemas em todos os aspectos do negócio.
Heijunka, ou Nivelamento de Produção, é um conceito que se originou no Sistema Toyota de Produção e não tem um único criador. Taiichi Ohno, engenheiro e executivo da Toyota, desempenhou um papel fundamental na concepção e implementação do Sistema Toyota de Produção, e o conceito de Heijunka é uma parte fundamental dessa abordagem.
Heijunka é a prática de nivelar a produção ao longo do tempo, distribuindo igualmente a carga de trabalho e a demanda do cliente entre os recursos disponíveis. Isso é feito para reduzir a variabilidade, melhorar a eficiência e minimizar o desperdício, permitindo uma produção mais enxuta e ágil. Heijunka é frequentemente usado em conjunto com o sistema Kanban para gerenciar a produção e o fluxo de materiais.
A conexão entre Heijunka e a filosofia Kaizen se estabelece através do objetivo compartilhado de melhoria contínua e eliminação de desperdícios. Heijunka contribui para a melhoria contínua ao criar um ambiente de produção mais estável e previsível, facilitando a identificação e solução de problemas.
O Heijunka tornou-se uma ferramenta da filosofia Kaizen nas décadas de 1980 e 1990, quando a filosofia Lean e o Sistema Toyota de Produção se difundiram globalmente. Desde então, o Heijunka tem sido adotado por organizações de diversos setores como uma prática essencial para implementar com sucesso a filosofia Kaizen e melhorar a eficiência e a eficácia de seus processos de produção.
Filosofia Kaizen e Sistema Toyota de Produção
Sim, é correto afirmar que a filosofia Kaizen tem suas raízes no Sistema Toyota de Produção. Muitos dos conceitos e ferramentas associados à filosofia Kaizen, como a melhoria contínua, a eliminação de desperdícios, e o envolvimento de todos os funcionários no processo de melhoria, foram inicialmente desenvolvidos e aplicados pela Toyota em sua abordagem de fabricação.
O Sistema Toyota de Produção foi criado por Taiichi Ohno e outros colaboradores na Toyota durante as décadas de 1940 e 1950 como uma resposta aos desafios enfrentados pela indústria automobilística japonesa após a Segunda Guerra Mundial. Esta abordagem de fabricação enxuta enfatiza a eficiência, a qualidade e a responsabilidade compartilhada na busca por um melhor desempenho e satisfação do cliente.
A filosofia Kaizen, que significa “melhoria contínua” em japonês, foi adotada e refinada por várias organizações japonesas além da Toyota e, eventualmente, ganhou destaque e reconhecimento global como uma abordagem eficaz para a melhoria contínua dos processos e resultados de negócios.
Embora a filosofia Kaizen tenha se originado no Sistema Toyota de Produção, ela foi ampliada e adaptada para diversos setores e tipos de organizações, tornando-se uma abordagem mais ampla para a gestão da qualidade e melhoria contínua.